AlteredEgo
Active Member
Hello Ya'll! I am in the southwest, and we have loads of sun, so I have been doing a grow this year using the sun through a textured window, and I noted the days shorter than 12 hrs, and lots of cloudy days this year. I needed some supplementary lighting. Being a fabricator at heart, and on a budget of disability income, I started thinking and studying lighting, wavelengths of light, and plant needs etc. I decided since I am flowering now, but might want to mix or change tight types, I decided on CFL's. I thought I'd need a great reflector to direct this light, and enhance the ability of CFL's to project light a little ways from the bulbs, so it can reach a ways.
Then, I decided to put a little bit of HPS in it, along with the CFL's, and use the mix of lighting, with 4 2700K CFL's, 2 6500k CFL's, and a 70W HPS. One of my primary objectives in this project was to be able to easily upgrade at a later time, if needed. Also, I have designed and assembled large commercial control panels, and done residential and commercial wiring, as well as teaching refrigeration, so I have the knowledge and skills to do a proper job, with safety as well as function observed.
I will be describing here, in possibly too much detail how I built this light, and how it evolves as I get to the remaining steps in getting it the way I planned it. There may surely be changes in design as I use the light, and learn how it performs, and yes, there will/should be a grow journal along with this.
Remember, I am using lighting plus sunlight, but indoors and secret for now, even though my state has provision for MMJ at this point. So, get onboard, and let's build a light, that starts out cheap, and where from there? Who knows!
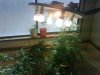
From the pic you can see this light does very well upside the south facing window, and I am using about 250w of power, with efficiency losses, to run this low heat, power company friendly light.
Oh yeah, the light is not finished in this photo, so, as I said, it will evolve.
Then, I decided to put a little bit of HPS in it, along with the CFL's, and use the mix of lighting, with 4 2700K CFL's, 2 6500k CFL's, and a 70W HPS. One of my primary objectives in this project was to be able to easily upgrade at a later time, if needed. Also, I have designed and assembled large commercial control panels, and done residential and commercial wiring, as well as teaching refrigeration, so I have the knowledge and skills to do a proper job, with safety as well as function observed.
I will be describing here, in possibly too much detail how I built this light, and how it evolves as I get to the remaining steps in getting it the way I planned it. There may surely be changes in design as I use the light, and learn how it performs, and yes, there will/should be a grow journal along with this.
Remember, I am using lighting plus sunlight, but indoors and secret for now, even though my state has provision for MMJ at this point. So, get onboard, and let's build a light, that starts out cheap, and where from there? Who knows!
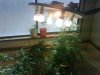
From the pic you can see this light does very well upside the south facing window, and I am using about 250w of power, with efficiency losses, to run this low heat, power company friendly light.
Oh yeah, the light is not finished in this photo, so, as I said, it will evolve.
Attachments
-
89.7 KB Views: 53
-
70.6 KB Views: 40
-
74.7 KB Views: 45